Most commonly used environmentally friendly materials for vacuum insulated water bottles are 304 stainless steel and 316 stainless steel. Both 304 stainless steel and 316 stainless steel are very healthy and environmentally friendly materials, with only minor differences. Here comes some comparison.
Material Characteristics304 stainless steelAs the most widely used stainless steel, it is used in food equipment, general chemical equipment, atomic energy industry, etc.; high ductility, corrosion resistance, heat resistance, low temperature strength, good mechanical properties; deep drawing, bending and other normal temperature processing properties Preferably, it does not harden after heat treatment; non-magnetic; use temperature: -196 to 800 °C.316 stainless steelMo is added, which is particularly resistant to corrosion, air corrosion and high temperature, and is suitable for use in harsh conditions. Work hardening performance is good. Seawater equipment, chemicals, paper, fertilizer production equipment, photography, food industry.The following is a comparison of the two materials.
Type 304 stainless steel 316 stainless steelCorrosion Resistance Good ExcellentDuctility Good GoodWelding Performance Excellent ExcellentRaw Material Price About CNY20/KG About CNY30/KGMaterial Processing Technology and CharacteristicsProcessing technology304 is welded with H0Cr21Ni10, solution treatment after welding;316 is welded with H0Cr19Ni12Mo2, solution treatment at 1050-1100 degrees Celsius after welding;Welding Characteristics (304 and 316)
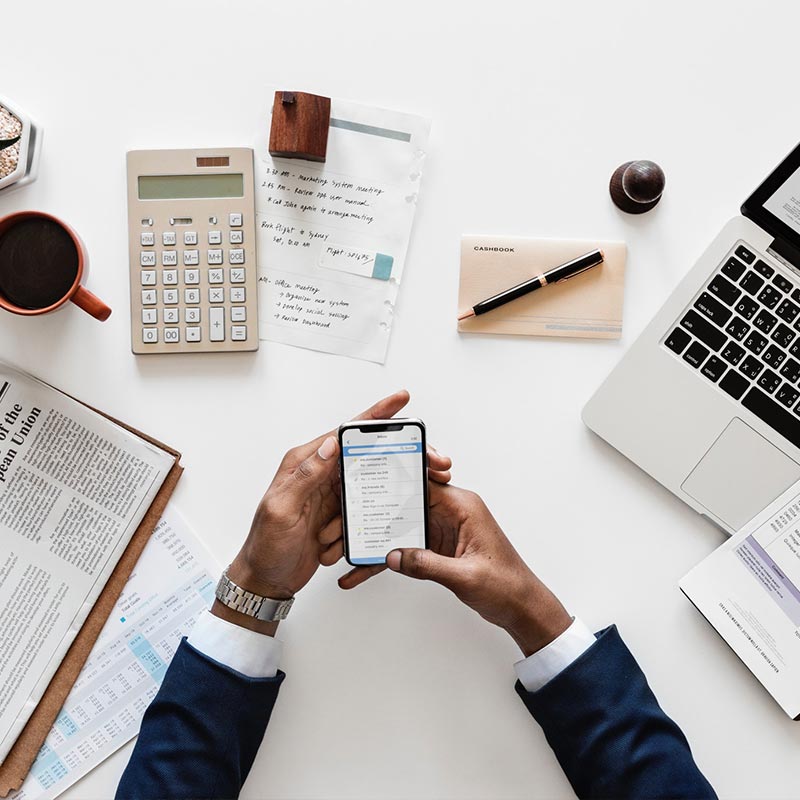
1. Brazing heating temperature is low, the joint is smooth and flat, the structure and mechanical properties change little, the deformation is small, and the workpiece size is accurate.
2. Weldable dissimilar metals can also be welded to dissimilar materials, and there is no strict limit on the thickness difference of the workpiece.
3. Some brazing methods can weld multiple weldments and multiple joints at the same time, and the productivity is high.
4. The brazing equipment is simple and the production investment cost is small.
5. The joint strength is low, the heat resistance is poor, and the pre-weld cleaning requirements are strict, and the brazing material is expensive.